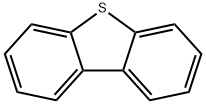
Dibenzothiophene synthesis
- Product Name:Dibenzothiophene
- CAS Number:132-65-0
- Molecular formula:C12H8S
- Molecular Weight:184.26
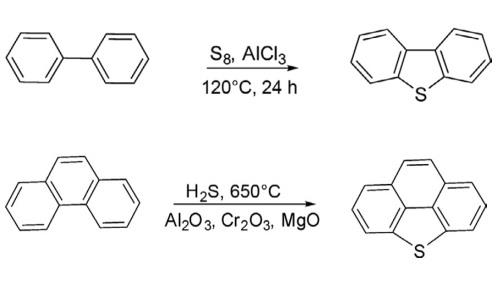
The parent dibenzothiophene has been synthesized by heating a mixture of biphenyl with sulfur at 120°C for 24 h in the presence of anhydrous AlCl3 in 79% yields. This methodology is useful for the synthesis of substituted dibenzothiophenes.
An alternative new protocol has been developed for the synthesis of dibenzothiophene and bridged dibenzothiophene by heating diphenyl and phenanthrene separately with H2S in the presence of mixed metal oxides (Al2O3, Cr2O3, and MgO) at 650°C.
![Carbamothioic acid, dimethyl-, O,O'-[1,1'-biphenyl]-2,2'-diyl ester (9CI)](/CAS/20210305/GIF/81056-07-7.gif)
81056-07-7
0 suppliers
inquiry
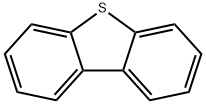
132-65-0
377 suppliers
$6.00/5g
Yield:132-65-0 99.1%
Reaction Conditions:
in toluene at 340; under 112511 Torr; for 4 h;Flow reactor;High pressure;Newman-Kwart Rearrangement;Temperature;Pressure;Time;
Steps:
7 Synthesis of dibenzothiophene by flow reactor
O, O '- (1,1'-biphenyl) -2,2'-diylbis (dimethylthiocarbamate) was carried out using the flow reactor 10 shown in FIG. In the section of the heating section 13, a tube 11 having an inner diameter of 1.0 mm (outer diameter of 1/16 inch, 1.59 mm) and a length of 10 m, an inner diameter of 2.17 mm (outer diameter of inch, 3.18 mm), a length The tube 11 of 20 m in length was connected and used. In the section of the cooling section 14, a tube 11 having an inner diameter of 1.0 mm (outer diameter of 1/16 inch, 1.59 mm) and a length of 2 m was used. For the fitting 16 of the tube 11, a tube joint manufactured by Swagelok Company was used. The pump 12 used NP-KX-520 type double plunger pump manufactured by Nippon Seimitsu Kagaku Kabushiki Kaisha, and the back pressure valve 15 used an airload type back pressure valve made by Tescom. A tube was inserted into a thermostatic chamber of a gas chromatograph manufactured by Shimadzu Corporation and used as a heating part 13, and the heating part 13 was set at a predetermined reaction temperature. The cooling unit 14 cooled by air cooling.O, O '- (1,1'-biphenyl) -2,2'-diylbis (dimethylthiocarbamate) was dissolved in 460.95 mL of toluene to prepare a 1.0 wt% raw material solution. And was sent to the flow reactor 10 using a double plunger pump of NP-KX-520 manufactured by Nippon Seimitsu Kagaku K.K. The liquid feed rate of the raw material solution was set to 0.25 mL / min, and the reaction solution was cut off in the sampling tube for the first 4 hours until the composition became stable and then collected. The obtained reaction solution was analyzed by GC and the yield was calculated.
References:
JP2017/137244,2017,A Location in patent:Paragraph 0046-0048
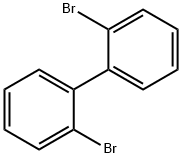
13029-09-9
286 suppliers
$20.00/1g
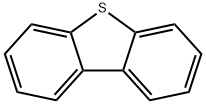
132-65-0
377 suppliers
$6.00/5g
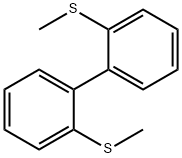
7343-32-0
1 suppliers
inquiry
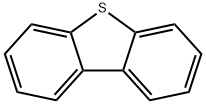
132-65-0
377 suppliers
$6.00/5g
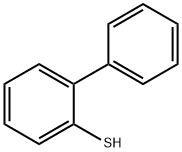
2688-96-2
50 suppliers
$430.00/1g
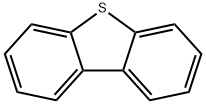
132-65-0
377 suppliers
$6.00/5g