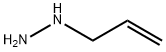
ALLYLHYDRAZINE synthesis
- Product Name:ALLYLHYDRAZINE
- CAS Number:7422-78-8
- Molecular formula:C3H8N2
- Molecular Weight:72.11
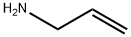
107-11-9
1 suppliers
$26.00/25ml
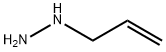
7422-78-8
23 suppliers
inquiry
Yield: 80%
Reaction Conditions:
with sodium hydroxide;chloroamine in water at 35 - 45;
Steps:
EXAMPLE Continuous Preparation of the Monoallylhydrazine; All of the quantities indicated correspond to a unit system and are in relation to a liter of hypochlorite injected. One liter of a sodium hypochlorite solution elaborated by the dilution of 50% of a high-concentration hypochlorite solution (100-120° chlorometric, which is after dilution [NaOCl]=2.14 mol/l and [NaCl]=0.85 mol/l) and a liter of a solution having an ammonia concentration of 3.60 mol/l and an ammonium chloride concentration of 2.38 mol/l are each introduced continuously into a stirred reactor (R1) at a rate of 5 ml/min (which is 6 g/min of the 480 chlorometric hypochlorite solution and 5.05 g/min of the NH3+NH4Cl ammonia mixture). The temperature within the reactor is maintained in the range between -8 and -11° C., and the pH of the reaction is approximately 10. Upon removal from R1, a monochloramine solution of a concentration greater than 1 mol/l is obtained, which corresponds to a yield near 100% with respect to the sodium hypochlorite. Upon removal from R1, the monochloramine solution obtained above (2 liters) is alkalized by the continuous introduction of a concentrated solution of sodium hydroxide (0.39 liter at 30% by weight) into a double-wall mixer (M) maintained at a low temperature in the range between -9 and -11° C. Homogenization is ensured by a magnetic drive. The synthesis of the monoallylhydrazine is carried out by means of a stirred tubular reactor (R2). The alkalized monochloramine (2.39 liters), arising from the container of the mixer M, and the anhydrous allylhydrazine (3.25 liters, which is 2.46 kg due to its density of 0.760) are introduced simultaneously at the base of the reactor by means of metering pumps. The flow rate of the anhydrous allylhydrazine is 16.46 ml/min and a part of the reaction is carried out in a homogeneous medium at 35° C. The final concentration in NaOH upon exit from R2 is 0.3 mol/l. This present method is characterized such that the sodium hydroxide is added to the homogeneous reaction liquor (5.6 kg) according to a weight concentration preferably in the range between 30% and 40% and under cooling so that the temperature does not exceed 45° C. Under these conditions, two phases are obtained, one of which, the light phase (approximately 2 kg), contains the totality of the organics, that is to say, the monoallylhydrazine and the excess allylamine. This treatment thus makes it possible to eliminate between 80% and 85% by weight of the water present in the synthesis solutions. Obtaining the monoallylhydrazine then requires two successive steps: Recovery of the unreacted allylamine by the distillation of the phase at atmospheric pressure. Approximately 1.7 kg of anhydrous amine is recovered at a temperature of 52° C. (distilling column CD1), which is reinjected without treatment into the reactor R2. Purification of the solution obtained in the base of the column (distilling column CD2) after separation by the addition of sodium hydroxide (40% to 50%). Before purification, the light phase has a concentrat-on in monoallylhydrazine of at least 95%. After purification, the monoallylhydrazine having a degree of purity greater, than 99% is obtained. The yield in the monoallylhydrazine with respect to the allylamine consumed is greater than 80%.
References:
Delalu, Henri;Colas-Duriche, Cecile;Berthet, Jacques;Leurent, Philippe US2007/185351, 2007, A1 Location in patent:Page/Page column 3-4
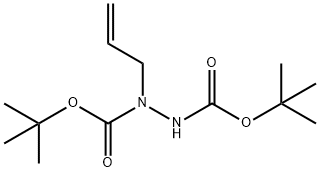
202980-98-1
1 suppliers
inquiry
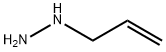
7422-78-8
23 suppliers
inquiry
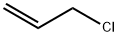
107-05-1
411 suppliers
$16.80/100ML
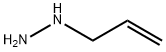
7422-78-8
23 suppliers
inquiry
![Ethanamine, N-[(3,5-dichlorophenyl)methylene]-2,2-diethoxy-](/CAS/20210305/GIF/1000210-73-0.gif)
1000210-73-0
0 suppliers
inquiry
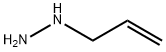
7422-78-8
23 suppliers
inquiry