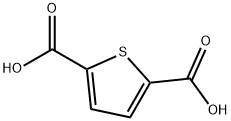
2,5-Thiophenedicarboxylic acid synthesis
- Product Name:2,5-Thiophenedicarboxylic acid
- CAS Number:4282-31-9
- Molecular formula:C6H4O4S
- Molecular Weight:172.16
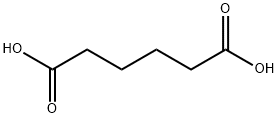
124-04-9
1012 suppliers
$6.00/25g
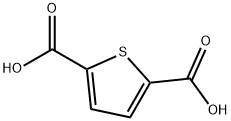
4282-31-9
343 suppliers
$6.00/5g
Yield:4282-31-9 75.58%
Reaction Conditions:
Stage #1:Adipic acid with dmap;thionyl chloride at 78 - 81; for 3.5 h;Large scale;
Stage #2: with sodium hydroxide in water; pH=9.3 - 10 at 70 - 72; for 2 h;Large scale;Reagent/catalyst;Temperature;pH-value;
Steps:
1; 2; 3; 4; 5; 6; 7; 8; 9 Example 1
A process for preparing an OB acid, comprising the steps of: 1, Check the synthesis reactor. All pipelines and valves are intact. Will have been cleaned of the reactor and the condenser in the case of exhaust gas drying. The temperature was then lowered to 40 ° C. 2, Open the manhole cover. Into the reactor, 365 kg of adipic acid and 8 kg of 4-dimethylaminopyridine were charged under vacuum. Cover the manhole cover. 3500 kg of thionyl chloride was vacuumed. 3, After feeding, after standing for 6 min, open the reactor jacket and condenser cooling water. Stir in the exhaust vent conditions 0.5h. 4, Jacket into the cold water. Improved steam. Heat the mixture with hot water. 5, The material temperature was increased to 78 ° C (15 ° C / h) for 3.5 h. 6, Between 78 ~ 81 ° C and maintain a good reflux. 7, After the reflux of the thionyl chloride, row of jacket hot water. Into the steam slowly warming. With 21h time, the material temperature was raised to 110 ° C at an average rate of 3 ° C / h. Excessive release of thionyl chloride was initiated. 8, After the temperature was increased to 120 ° C, the pressure was reduced by vacuum distillation using a water jet pump. Continue to discharge high-boiling-point by-products such as sulfur chloride. The temperature was then raised to 138 ° C to maintain the temperature. 9, Started to maintain temperature. Start the distillation water jet vacuum pump. The distillation system is preheated. To be maintained temperetaure to end. Discharge into the distillation kettle. 10, After all of the synthetic materials were transferred to a still kettle, open the receiving tank jacket cooling water. Start distilling kettle stirring. Under the action of water jet vacuum pump, the material temperature was slowly raised to 165 ° C over a period of 1.5 h. Gradually speed up the heating rate. Increase the vacuum to 0.07MPa. The acid chloride was distilled under reduced pressure to distillate-free. 475 kg of acid chloride was obtained. 11, Open the decolorization kettle vacuum valve. The distillated acid chloride was heated to 70 ° C and 100 kg of water was added dropwise. The acid chloride was hydrolyzed to a completely solid. Add water to 2500L. Dropping 30% concentration of liquid sodium hydroxide, so that the solution pH value of 10. Jacket into the steam heated to 72 ° C and heat 2h. Re-test the pH value of 9.3. Cooled to 40 ° C. Transferred into the bleaching kettle. The pH of the solution was adjusted to 6.0 by the addition of hydrochloric acid. Stir until it is stable. Stop mixing. Into the kettle into the activated carbon. Decolorized with stirring at 80 ° C for 1 h. Into the cold water to 30 ° C. The solution was filtered through a filter. 12, Filtration of the filtrate into the acidification reactor. Dropping hydrochloric acid under stirring to bring the pH value of the solution to 2.0. Stirring 15min. Re-test with a precision test strip after feeding into the centrifuge rejection rejection filter. Filtrate into the sedimentation tank. The filter cake was dried and weighed. Was crude 365kg. 13, 11 times the weight of the crude product obtained, the crude product is put into a refining kettle under the action of stirring. Cover the man hole cover. Jacket over the steam quickly heated to reflux. Side by side hot water jacket to improve the cold water quickly cooled to 45 ° C filtration. Was refined products. 14, Will be refined after two refined products into enamel double cone dryer. Open the steam and vacuum. The baking was carried out at 110 ° C for 4.5 h under reduced pressure. The vacuum degree is 0.08MPa. After sampling analysis, moisture ≤ 0.20% qualified. Cooling. Remove the cold after crushing packaging. The finished product obtained in this example was 325 kg. HPLC analysis of the content of 99.13%. Yield: 75.58%.
References:
Sichuan Yuntong Chemical Industry Co., Ltd.;Shi, Yi;Li, Zongjun;Mai, Qing CN105906606, 2016, A Location in patent:Paragraph 0022-0148
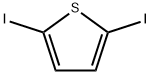
625-88-7
122 suppliers
$16.00/1g
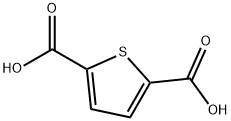
4282-31-9
343 suppliers
$6.00/5g
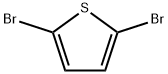
3141-27-3
309 suppliers
$5.00/10g
201230-82-2
1 suppliers
inquiry
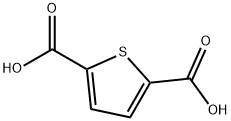
4282-31-9
343 suppliers
$6.00/5g
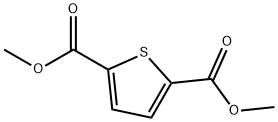
4282-34-2
54 suppliers
$85.00/250 mg
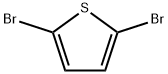
3141-27-3
309 suppliers
$5.00/10g
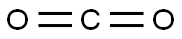
124-38-9
129 suppliers
$175.00/23402
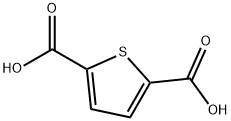
4282-31-9
343 suppliers
$6.00/5g
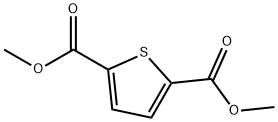
4282-34-2
54 suppliers
$85.00/250 mg
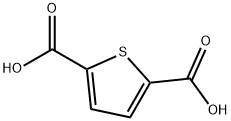
4282-31-9
343 suppliers
$6.00/5g