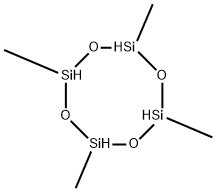
2,4,6,8-Tetramethylcyclotetrasiloxane synthesis
- Product Name:2,4,6,8-Tetramethylcyclotetrasiloxane
- CAS Number:2370-88-9
- Molecular formula:C4H16O4Si4
- Molecular Weight:240.51
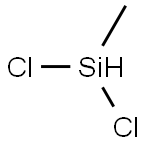
75-54-7
169 suppliers
$32.47/25G
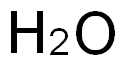
7732-18-5
469 suppliers
$12.69/100ml
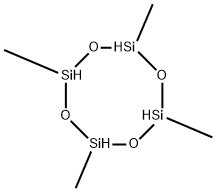
2370-88-9
258 suppliers
$17.00/5g
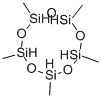
6166-86-5
47 suppliers
$95.00/2.5ml
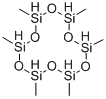
6166-87-6
4 suppliers
inquiry
Yield:-
Reaction Conditions:
Stage #1:Dichloromethylsilane;water at 33; under 3863.02 Torr;
Stage #2:dodecylbenzenesulphonic acid in isopar P at 20; for 3 h;
Steps:
1
Methyldichlorosilane CH3SICL2 was mixed with a stoichiometric equivalent of water, i. e. 0.5 mole of water per mole of silicon bonded chlorine, in a steam heated continuous hydrolysis reactor. The hydrolysis reactor was maintained at 60 psig and the temperature of the reactor was controlled such that the hydrolyzate exiting the reactor was at a temperature of about 33°C. The hydrolyzate exiting the reactor was analysed by gas chromatography (GC) using a flame ionisation detector (FID) and found to comprise about 95 weight percent linear chlorine end-terminated methylhydrogensiloxane species and about five weight percent cyclic methylhydrogensiloxanes species. The hydrolyzate was diluted to about 20% IN ISOPAR P'hydrocarbon solvent containing 0. 1% dodecylbenzenesulphonic acid catalyst. Excess HC1 gas from the hydrolysis reaction was collected for re-use. [0021] The diluted hydrolyzate containing catalyst was fed through a simple rearrangement reactor tank at ambient temperature and pressure. Residence time of the diluted hydrolyzate in the reactor was about 3 hours. GC-FID analysis of the product exiting the rearrangement reactor showed the siloxane component to consist of about 70 weight percent linear chlorine end-terminated methylhydrogensiloxane species and about 30 weight percent cyclic methylhydrogensiloxane species. [0022] The product from the rearrangement reactor was heated to drive off aqueous HC1, stripped in flash drums under vacuum and then vacuum distilled and the cyclic species and low-boiling linear species taken overhead. The bottom fraction was cooled and recycled to the rearrangement reactor. [0023] Residual chlorine in the overhead fraction from the flash distillation (the crude product) was removed by contact with a calcium carbonate calcium chloride water system. The product was finally dried in a magnesium oxide bed. The recovered cyclic methylhydrogensiloxane fraction was analysed by GC-FID and found to comprise 99.7 weight percent cyclic methylhydrogensiloxanes of the tetramer, pentamer, and hexamer species. The process was run continuously for about 20 days.
References:
DOW CORNING CORPORATION WO2005/5441, 2005, A2 Location in patent:Page/Page column 6; 7
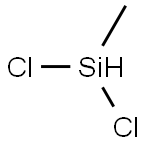
75-54-7
169 suppliers
$32.47/25G
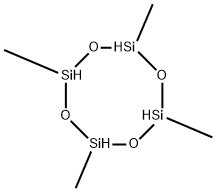
2370-88-9
258 suppliers
$17.00/5g
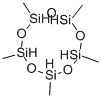
6166-86-5
47 suppliers
$95.00/2.5ml
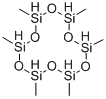
6166-87-6
4 suppliers
inquiry
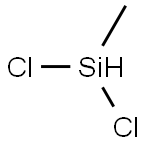
75-54-7
169 suppliers
$32.47/25G
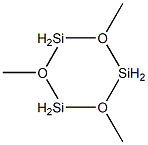
13269-39-1
14 suppliers
inquiry
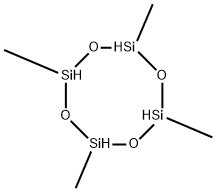
2370-88-9
258 suppliers
$17.00/5g
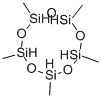
6166-86-5
47 suppliers
$95.00/2.5ml
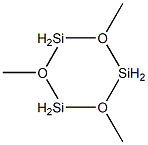
13269-39-1
14 suppliers
inquiry
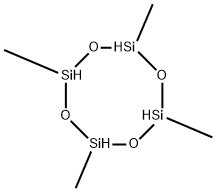
2370-88-9
258 suppliers
$17.00/5g
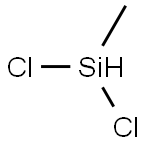
75-54-7
169 suppliers
$32.47/25G
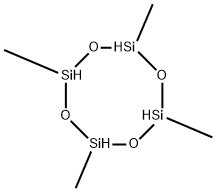
2370-88-9
258 suppliers
$17.00/5g