
4-Amino-1-butanol synthesis
- Product Name:4-Amino-1-butanol
- CAS Number:13325-10-5
- Molecular formula:C4H11NO
- Molecular Weight:89.14
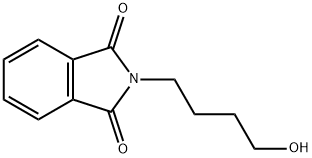
24697-70-9
38 suppliers
inquiry

13325-10-5
309 suppliers
$10.00/1g
Yield:13325-10-5 90.8%
Reaction Conditions:
with water;sodium hydroxide at 100; for 10 h;
Steps:
1.2-5.2
43.84 g of the intermediate N-(8-hydroxybutyl)phthalimide obtained in the step (1) was placed in a 250 ml three-necked flask, and then 200 ml of water and 16 g of solid sodium hydroxide were successively added. Mix and stir evenly; then heat and reflux at 100 ° C for 10 hours until the end of the reaction, after the end of the reaction to obtain a mixed solution of 4-aminobutanol; the resulting mixture of 4-aminobutanol was cooled to room temperature, with 6 mol / L hydrochloric acid adjusts the pH of the 4-aminobutanol mixed solution to 10, and then extracts the organic phase of the 4-aminobutanol mixed solution with chloroform solution, extracts twice, uses 100 ml of chloroform each time, and uses 50 ml of saturated sodium chloride solution. The organic phase after the extraction is washed, and after washing, anhydrous sodium sulfate is added for drying; after the drying is completed, the dried solution is first subjected to rotary evaporation to remove the chloroform by a rotary evaporator, and then the oil pump is used at a temperature of The rectification treatment is carried out under conditions of 94±2° C. and a pressure of 0.6 to 0.7 kPa, and after completion of the rectification treatment, the product is cooled to room temperature to obtain a product of 4-aminobutanol. The obtained product 4-aminobutanol had a mass of 16.23 g, a yield of 90.8%, and a purity of 99.5%.
References:
CN108658792,2018,A Location in patent:Page/Page column 5-9

110-63-4
701 suppliers
$24.80/250g

13325-10-5
309 suppliers
$10.00/1g
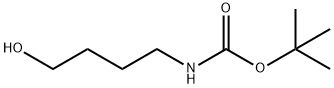
75178-87-9
122 suppliers
$6.00/100mg

13325-10-5
309 suppliers
$10.00/1g

110-63-4
701 suppliers
$24.80/250g

123-75-1
543 suppliers
$10.00/5g
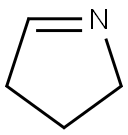
5724-81-2
9 suppliers
inquiry

13325-10-5
309 suppliers
$10.00/1g

110-60-1
188 suppliers
$10.00/1g

110-63-4
701 suppliers
$24.80/250g

123-75-1
543 suppliers
$10.00/5g
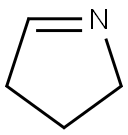
5724-81-2
9 suppliers
inquiry

13325-10-5
309 suppliers
$10.00/1g