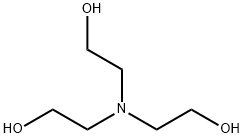
Triethanolamine synthesis
- Product Name:Triethanolamine
- CAS Number:102-71-6
- Molecular formula:C6H15NO3
- Molecular Weight:149.19
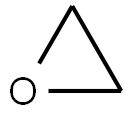
75-21-8
229 suppliers
$39.10/1mL
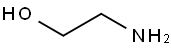
141-43-5
878 suppliers
$9.00/10g
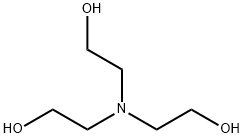
102-71-6
774 suppliers
$18.00/100g

111-42-2
834 suppliers
$10.00/20mg
Yield:102-71-6 91.1% ,111-42-2 7.6%
Reaction Conditions:
with ammonia;ZSM-5 type zeolite ion exchange with lanthanum at 45; under 75007.5 Torr;Industry scale;Adiabatic conditions;
Steps:
II-1 EXAMPLE II-1
In a plant for producing ethanolamine, the catalyst process was implemented by continuously introducing EO, liquid ammonia, and MEA into a reactor packed with a catalyst at such flow rates as to enable their concentrations to reach 18.1, 70.9, and 11.0% by weight respectively. The reaction was performed adiabatically at a reaction pressure of 10 MPa, at an inlet temperature of 45°C and at a LHSV of 5.9. The catalyst used was a ZSM-5 type zeolite which had undergone ion exchange with lanthanum. The aqueous ammonia process was implemented by continuously introducing EO and an aqueous 37% ammonia solution into another reactor at such flow rates as to enable the molar ratio of EO and ammonia to reach 0.28. The degree of conversion of EO at the plant for the production of ethanolamine by the catalyst process and the aqueous ammonia process was nearly 100%. The reaction solution consequently obtained was deprived of the unaltered ammonia of the catalyst process by the pressure distillation. The remaining solution and the reaction solution of the aqueous ammonia process were mixed together. The mixing ratio (weight) of catalyst process/aqueous ammonia process was 60/40. Fig. 4 is a diagram schematically illustrating a flow of the operation of distilling the reaction solution. In Fig. 4, a reaction solution 401 (a mixture of the solutions of the catalyst and aqueous ammonia processes) was first distilled continuously in an ammonia stripping column 402 to distill aqueous ammonia, then continuously distilled in a dehydrating column 403 to distill water, continuously distilled in a MEA rectifying column 404 to distill MEA, and further distilled continuously in a DEA rectifying column 405 to distill DEA and obtain the raw material TEA in the form of bottoms. The bottoms had a composition formed of 91. 7% by weight of TEA, 7.6% by weight of DEA, and 0.7% by weight of high-boiling compounds. In Fig. 4, the raw material TEA and a low-boiling compound 408 were mixed together and fed to a TEA rectifying column 406, batch distillation, to distill TEA. Specifically, a 500 g portion of the bottom (raw material TEA) and 15 g of distilled water were mixed together and the resultant mixture was placed in a 600 ml three-neck flask made of glass and furnished with a capillary tube and given therein thorough displacement with nitrogen gas. Thereafter, the resultant mixture was heated and vacuumized, treated under the conditions of 90°C - 170°C/400 - 10 hPa to expel water, and thereafter distilled under the conditions of 160°C - 167°C . Consequently, TEA having a purity of 99.7% by weight was obtained in an amount of 300 g (yield 59.9%). Incidentally, the distillation was performed by introducing a forced current of nitrogen gas via the capillary tube into the reactor. The refined TEA obtained consequently was tested for APHA. The results are shown in Table 16. The absorbance of the resultant TEA determined by the phosphorus coloration test was 0.09, 0.03, and 0.03 at wavelengths of 420, 510, and 530 nm respectively. The sample had a colorless transparent appearance free of suspended matter and a small of slight fragrance and not of pungent odor. The aging test showed a change of APHA from 20 to 25.
References:
EP1443036,2004,A1 Location in patent:Page 26
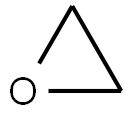
75-21-8
229 suppliers
$39.10/1mL

111-42-2
834 suppliers
$10.00/20mg
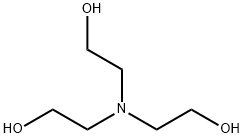
102-71-6
774 suppliers
$18.00/100g
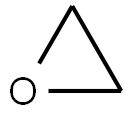
75-21-8
229 suppliers
$39.10/1mL
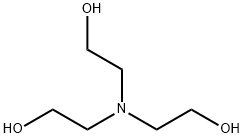
102-71-6
774 suppliers
$18.00/100g
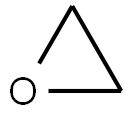
75-21-8
229 suppliers
$39.10/1mL
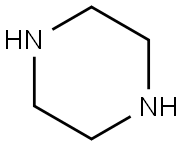
110-85-0
563 suppliers
$5.00/5G
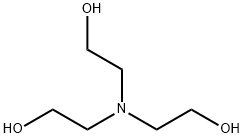
102-71-6
774 suppliers
$18.00/100g
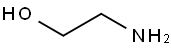
141-43-5
878 suppliers
$9.00/10g
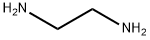
107-15-3
9 suppliers
$11.19/25ML
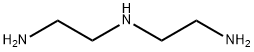
111-40-0
505 suppliers
$13.44/25ML

111-42-2
834 suppliers
$10.00/20mg
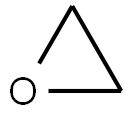
75-21-8
229 suppliers
$39.10/1mL
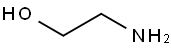
141-43-5
878 suppliers
$9.00/10g
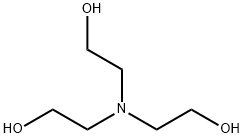
102-71-6
774 suppliers
$18.00/100g