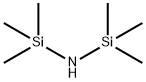
Hexamethyldisilazane synthesis
- Product Name:Hexamethyldisilazane
- CAS Number:999-97-3
- Molecular formula:C6H19NSi2
- Molecular Weight:161.39
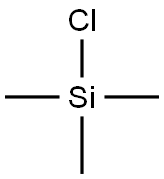
75-77-4
575 suppliers
$5.04/10
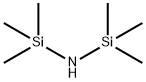
999-97-3
644 suppliers
$9.00/5G
Yield:999-97-3 97.3%
Reaction Conditions:
with ammonia at 50; under 1425.14 Torr; for 2.5 h;Temperature;Pressure;
Steps:
9
1 L of chlorotrimethylsilane was added to the reactor equipped with a stirrer, thermometer and pressure gauge. Stir well. Recanalize ammonia gas into the reaction. The total amount of ammonia gas was 1.6 L, the reaction temperature was controlled at 30°C, the reaction pressure is 0.15 Mpa, control reaction time is 0.5h, the rate of introduction of ammonia was 0.5 L / min. As the reaction progresses, more solid byproduct ammonium chloride is formed. Material gradually becomes a paste. Open the reactor bottom valve. Discharge processing. With the mortar pump to hit the reaction material within the frame filter press. The ammonium chloride solids are retained in the filter press. The clear liquid flow back to the reactor to continue the reaction in the manner described above. Circularly processed twice. The third time back to the reaction tank of clarified liquid reaction. The reaction mixture was removed from the reaction kettle. The reaction mixture was filtered. Remove the residue to obtain a filtrate. Finally, the obtained filtrate is analyzed and detected. The remaining amount of chlorotrimethylsilane in the filtrate was examined. The residual amount of chlorotrimethylsilane is brought to a predetermined value. The total time to complete the reaction was 2 h. After completion of the reaction, continue to fight the material filter. From the frame filter out of the clear liquid is no longer back to the reactor, but into the crude product receiving tank. Crude products after alkali washing to distillation, the product hexamethyldisilazane. The content of hexamethyldisilazane was 99.0% and the yield was 95.4% (molar yield).
In Examples 2-15, the reaction was carried out in the same manner as in Example 1 except changing trimethylchlorosilane, ammonia, the ammonia gas flow rate, reaction time, reaction temperature and reaction pressure. Specific formulations in Table 1. Specific process conditions, the amount of phase transfer catalyst and product yield are shown in Table 2.
Example 9; chlorotrimethylsilane 1.3 L; ammonia 2.14 L; ammonia gas flow rate 1.2 L / min
Example 9; Overall reaction time 2.5 h; Reaction temperature 50°C; Reaction pressure 0.19 MPa; Yield 97.3%
References:
CN105732688,2016,A Location in patent:Paragraph 0034; 0036; 0038; 0041

18306-29-1
107 suppliers
$13.00/5g
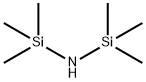
999-97-3
644 suppliers
$9.00/5G
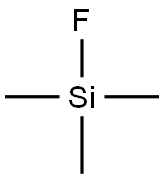
420-56-4
72 suppliers
$95.00/10g
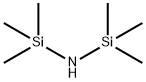
999-97-3
644 suppliers
$9.00/5G
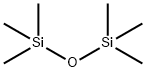
107-46-0
465 suppliers
$10.00/10g
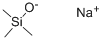
18027-10-6
119 suppliers
$66.00/1g
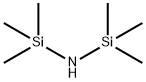
999-97-3
644 suppliers
$9.00/5G
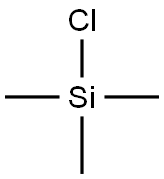
75-77-4
575 suppliers
$5.04/10
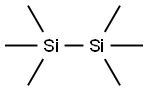
1450-14-2
292 suppliers
$29.12/10ML
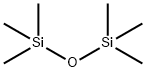
107-46-0
465 suppliers
$10.00/10g
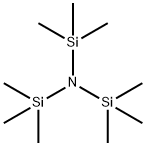
1586-73-8
95 suppliers
$55.00/5g
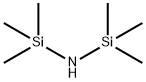
999-97-3
644 suppliers
$9.00/5G