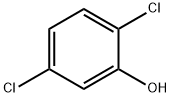
2,5-Dichlorophenol synthesis
- Product Name:2,5-Dichlorophenol
- CAS Number:583-78-8
- Molecular formula:C6H4Cl2O
- Molecular Weight:163
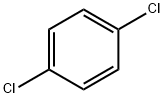
106-46-7
511 suppliers
$10.00/5g
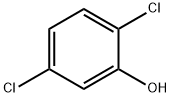
583-78-8
244 suppliers
$15.00/250 mg
Yield:583-78-8 80.9%
Reaction Conditions:
with peracetic acid;acetic acid at 30 - 75; for 6.5 h;Temperature;Reagent/catalyst;
Steps:
2 Example 2
0.01 part by weight of Fe5V8O27.5 and 0.1 part by weight of polyphosphoric acid were addedTo 1/10 parts by weight of acetic acid,It was stirred at 65 10min,After addition of 0.0071 × 10-3 parts by weight of peracetic acid,Stirring was continued for 20 min to obtain an activating liquid;1 part by weight of 1,4-dichlorobenzene and 12 parts by weight of acetic acid were stirred at a temperature of 30 ° C until the mixture was homogeneous,Then adding activating liquid to obtain reaction liquid;At a temperature of 75 ,0.017 parts by weight of peracetic acid was added dropwise to the reaction solution over a period of 6 hours,After completion of the dropwise addition,Stirring was continued for 0.5 h;Followed by the addition of 0.98 part by weight of sodium bisulfite,Stirring 5min, filtration, get filtrate;The filtrate was added at a rate of 9000 kg / hTo an evaporating kettle at a feed temperature of 35 ° C,The pressure was 550 kPa,To remove the mother liquor in the phosphoric acid,Coke tar, catalyst and other heavy components,For phosphoric acid, the recovery of the catalyst,The vapor phase out of the evaporation kettle enters the first rectification column,Wherein the feed flow rate is 8500 kg / h,The feed temperature was 100 & lt; 0 &The feed pressure was 45 kPa;The first distillation tower is a compound tower,The upper part is a 2-stage packed tower,The lower part is a partition plate having a number of stages of 30 plates,The top of the first distillation tower was discharged out of the waste water at a rate of 710 kg / h, and the mixture of acetic acid and water was withdrawn from the tower into the second distillation tower, the 1,4-dichlorobenzene and 2,5-dichlorophenol Of the mixture into the stripping column.The number of plates in the second distillation column was 60,The feed flow rate was 4000 kg / h,The feed temperature was 85 ° C and the pressure was 35 kPa.The second distillation column tower to 210kg / h speed out of wastewater, tower to 5500kg / h rate of recovery of acetic acid,Wherein the vapor phase separated from the top of the second rectification column is heated to the left side of the first rectification column separator,The condensate itself into a wastewater outflow, saving energy.The number of trays of the stripping column is 12 layers,The tower top gas phase enters the first rectification tower tower partition right tower tower cauldron,The tower bottom liquid enters the 1,4-dichlorobenzene purification tower at a flow rate of 1600 kg / h, wherein the 1,4-dichlorobenzene purification tower is a three-stage packed tower with a feed temperature of 150 ° C and a pressure of 45 kPa;1,4-dichlorobenzene purification tower overhead to 930kg / h speed out of 1,4-dichlorobenzene,The tower bottom liquid enters the third distillation tower with 500 kg / h,Wherein the third distillation tower is a three-stage packed tower,The feed temperature was 120 ° C and the pressure was 12 kPa.The third distillation column overhead light component returned to the 1,4-dichlorobenzene purification tower,The product was separated at a flow rate of 300 kg / h in the column2,5-dichlorophenol products, tower kettle out of heavy components,Return to the evaporation kettle.The final distillation of the productThe purity of 2,5-dichlorophenol was 99.7%The purity of the recovered acetic acid was 99.2%The purity of the recovered 1,4-dichlorobenzene was 99.3%In total, 0.35 parts of 2,5-dichlorophenol were obtained,0.61 parts of the raw material 1,4-dichlorobenzene was recovered,The yield of product 2,5-dichlorophenol (after deducting recovered raw materials) was 80.9%
References:
Jiangsu Lanfeng Biochemical Co., Ltd.;Ji, Chuanwu;Chen, Gaobu;Xu, Ning;Zhu, Qingyun;Fang, Jing;Huang, Xingyu;Kang, Li;Liu, Yu;Zhang, Xiangning CN104876805, 2016, B Location in patent:Paragraph 0045; 0046; 0047; 0048; 0049; 0050; 0051; 0052
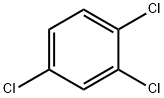
120-82-1
311 suppliers
$10.00/25g
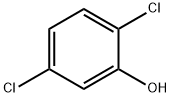
583-78-8
244 suppliers
$15.00/250 mg

1435-50-3
211 suppliers
$8.00/5g
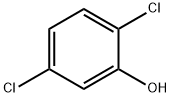
583-78-8
244 suppliers
$15.00/250 mg
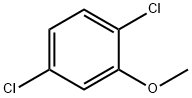
1984-58-3
108 suppliers
$6.00/1g
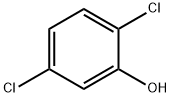
583-78-8
244 suppliers
$15.00/250 mg
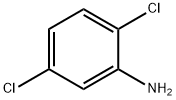
95-82-9
339 suppliers
$14.00/5g
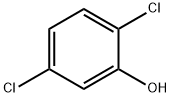
583-78-8
244 suppliers
$15.00/250 mg