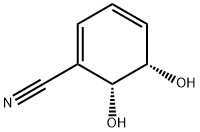
(+)-CIS-2(R),3(S)-2,3-DIHYDROXY-2,3-DIHYDROBENZONITRILE synthesis
- Product Name:(+)-CIS-2(R),3(S)-2,3-DIHYDROXY-2,3-DIHYDROBENZONITRILE
- CAS Number:138769-96-7
- Molecular formula:C7H7NO2
- Molecular Weight:137.14
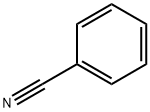
100-47-0
364 suppliers
$14.14/25gm:
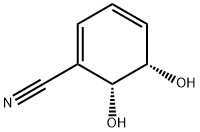
138769-96-7
6 suppliers
inquiry
Yield:> 99 % ee
Reaction Conditions:
with ammonium hydroxide in paraffin oil; pH=6.8;Microbiological reaction;
Steps:
4.2.3. Biotransformations in bioreactors
General procedure: Bioreactor cultures and biotransformations using E. coli JM109(pDTG601). Growth and biotransformation in the bioreactor usingE.coli JM109 (pDTG601) were carried out using a modification ofour previously published procedure.3b Thus, 5 mL of LB mediumsupplemented with ampicillin sodium salt (0.1 g/L) and glucose(5 g/L) were inoculated with a single colony of E. coli JM109(pDTG601), and grown overnight at 37 C and 150 rpm. Two500 mL shake-flasks containing 150 mL of MSB medium wereinoculated with 1 mL of the grown culture. These precultureflasks were placed in an orbital shaker at 37 C and 150 rpm, for12 hrs. Both entire cultures were used to inoculate the bioreactor(Sartorius Biostat A plus), charged with an initial volume of 2.5 L,and set to 500 rpm, 30 C, and air flow rate of 4L/min. The pHvalue was controlled automatically to 6.8 by addition of conc.ammonium hydroxide during the whole process. A pulse ofantifoam agents (Aldrich’s Antifoam Y: Silicone dispersion inwater 1:1) was added at the beginning of the run. At 6 h afterinoculation the dissolved oxygen value sharply increased(indicating carbon deprivation), whereupon a glucose fed-batchwas started by adding glucose (0.7 g/mL solution) from an initialrate of 0.08 mL/min to 0.54 mL/min in a 20 h period. When thebiomass concentration reached 15 g/L cdw, IPTG was added toinduce toluene dioxygenase expression (IPTG final concentrationin bioreactor of 10 mg/L), and the stirrer speed was set to900 rpm. After the culture reached the stationary phase (c.a.26 h, 50 g/L cdw aprox), glucose feeding was decreased to0.25 mL/min and substrate addition was started. A solution of thecorresponding substrate in liquid paraffin (0.5 M) was added at aflow rate of 20 mL/min using a peristaltic pump. After thebiotransformation was completed, the pH of the medium in thebioreactor was adjusted to 7.5. The culture broth was centrifugedat 7000 rpm and 4 C for 30 min, the supernatant was collectedand the cell pellet properly disposed. Centrifugation led to theseparation of the liquid paraffin (which contains no detectableamounts products) from the aqueous phase. The latter wasproperly lyophilized overnight to obtain a dry powder, whichwas extracted several times with ethyl acetate until no morediols were detected by TLC. The solvent was evaporated to affordthe corresponding diol, which was washed several times withhexanes to remove the liquid paraffin traces.
References:
Pazos, Mariana;Martínez, Sebastián;Vila, María Agustina;Rodríguez, Paola;Veiga, Nicolás;Seoane, Gustavo;Carrera, Ignacio [Tetrahedron Asymmetry,2015,vol. 26,# 24,p. 1436 - 1447]

591-50-4
484 suppliers
$10.00/1g
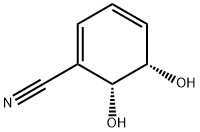
138769-96-7
6 suppliers
inquiry